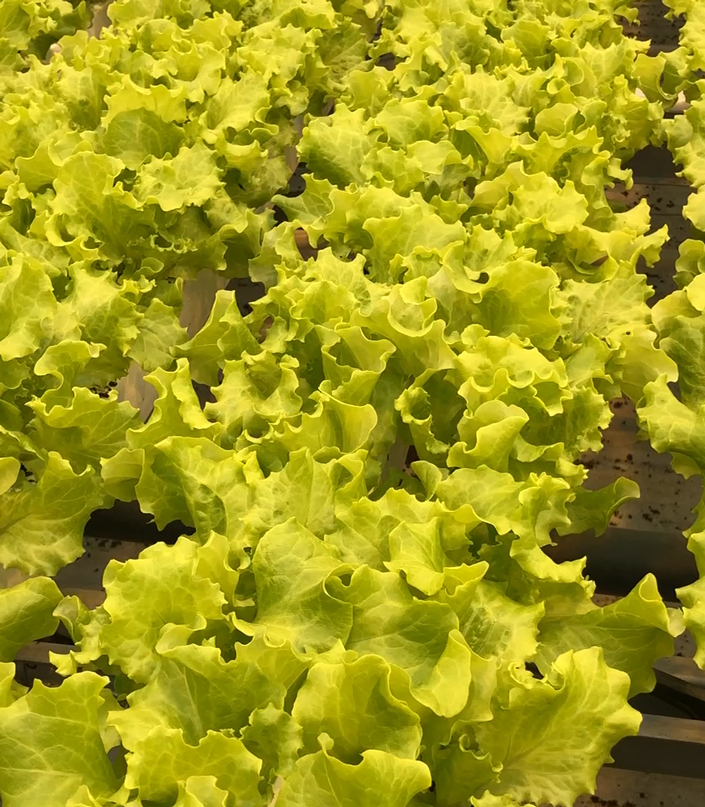
FRESH TASTY HARVEST 365 DAYS A YEAR
With traditional cultivation in open ground, usually 8 plants per m2 are grown per year. In salad lines, more than 1000 plants per m2 can be grown annually. Modern technologies allow for continuous production planning and forecasting the harvest for each day.
Lettuce, greens, herbs – all plants in the lines are tasty, beneficial, and ecologically clean. The assortment for cultivation is quite large: basil, lemon balm, arugula, dill, parsley, onion, iceberg, lollo rosso, romaine, lettuce, butterhead, oakleaf, baby leaf mustard, baby leaf radish (leaves only), baby leaf spinach, and other herbs.
3 key indicators of salad lines
EFFICIENT USE OF SPACE
Every meter of the greenhouse is used as efficiently as possible thanks to the special design of the tables, as well as the automatic sliding and arrangement of trays with plants.
EFFICIENCY OF LABOR
Take advantage of all the benefits of automation. Automated lines in the greenhouse minimize labor costs. From sowing to harvesting, almost no human labor is required.
EFFICIENT USE OF RESOURCES
The closed and controlled hydroponic system circulates irrigation water, reducing water consumption by 95% compared to soil cultivation.
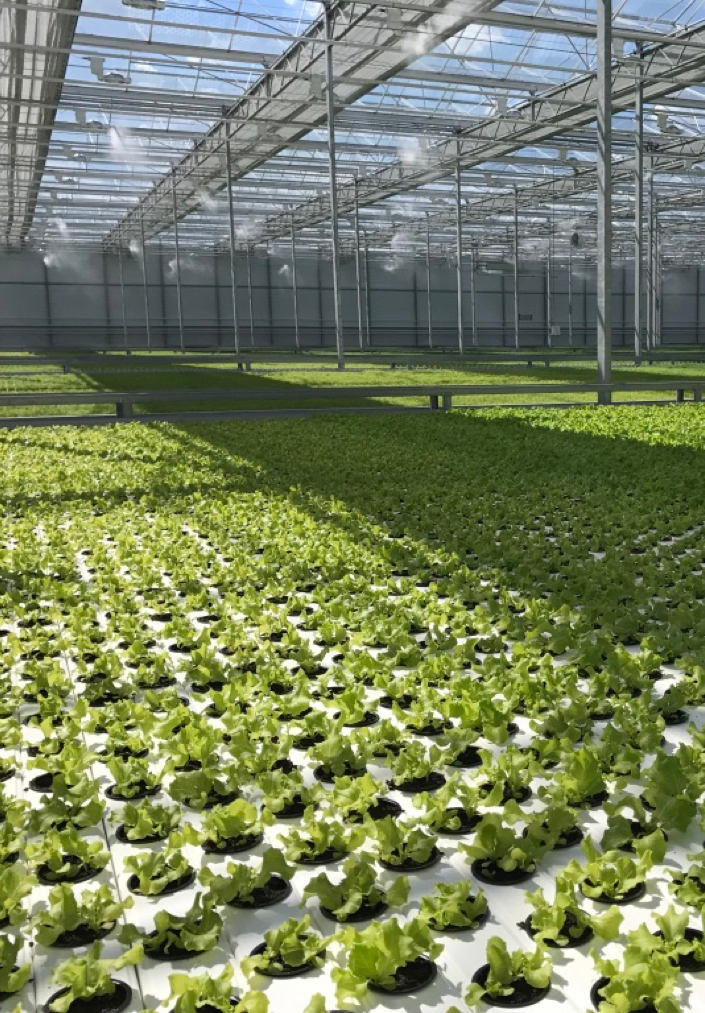
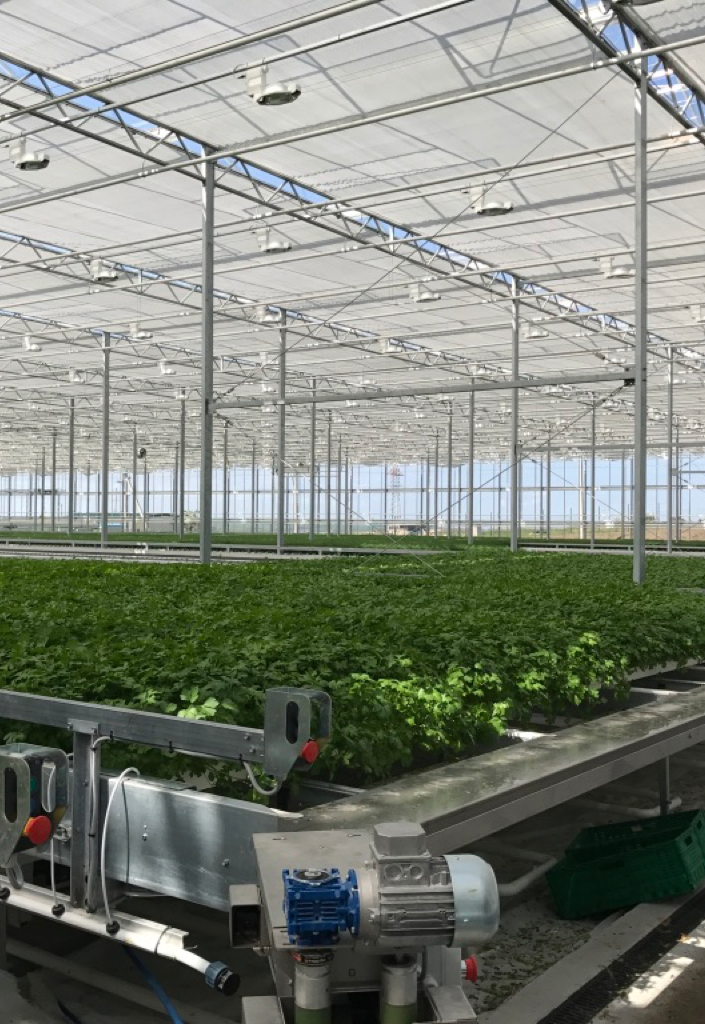
Certainly, this system stands out in its excellence! With its user-friendly interface, meticulous control, predictive features, and full-scale automation of essential operations, it's the pinnacle of what one can offer to businesses. Are you captivated? We don't just bring such projects to life; we meticulously craft detailed blueprints for each procedure.